Le Blog Bim
Besoin d’un conseil ?
Laissez-nous vos coordonnées afin qu’on puisse vous rappeler.
Je veux être contacté par un expertLe blog de BIM in Motion est dédié à l’innovation, au digital et à l’amélioration des performances des entreprises du secteur de la construction et de l’immobilier.
Ce blog intègre nos retours d’expériences, nos développements et de la veille technique autour du BIM & de la digitalisation du secteur.
Vous y trouverez une sélection de sujets d’actualité : Méthodes applicatives, outils, technologies, recherches & développements, systèmes d’organisations, partenariats, actualités… Tous ces avis d’experts mis à votre disposition pour faire bénéficier au réseau de l’évolution des pratiques.
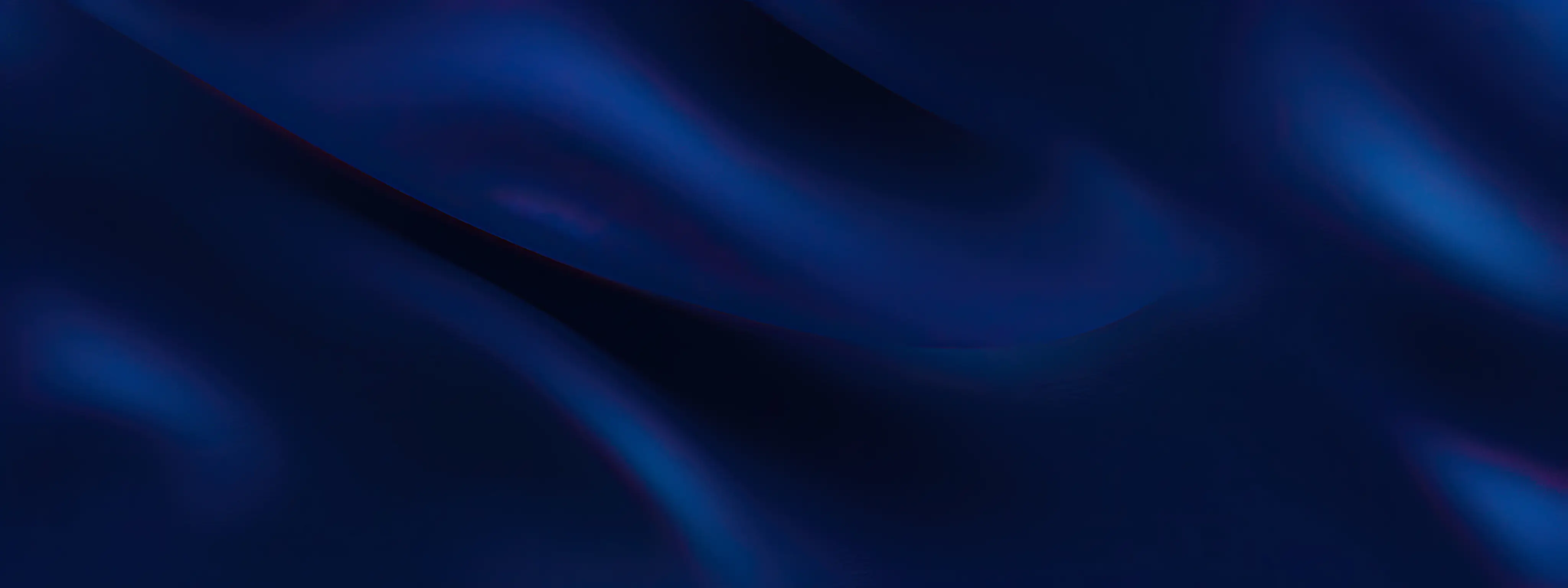
Recevez les dernières informations sur SOCOTEC, inscrivez-vous à notre newsletter !
Recevez les dernières informations sur SOCOTEC, inscrivez-vous à notre newsletter !
S'inscrire